Need more information about Rawlplug? go to brand site
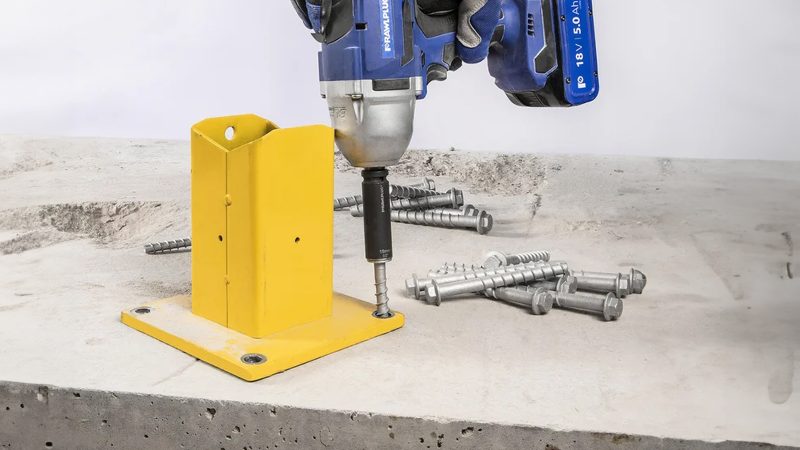
We have proven that fixing in concrete is our speciality. The new R-HLX concrete screw has recently joined our range of anchor and screw solutions.
The power of our solution is based on an innovative process of forging and heat treatment, ensuring the high grade and flexibility of the steel in the finished product. The new high-quality R-HLX concrete screws have been designed with a zinc-flake coating, guaranteeing extreme corrosion resistance, confirmed in a salt chamber test with a result of 15,000 hours!
The R-HLX concrete screw is a new quality of installation, guaranteed by a precisely developed form. Whether it is a new thread shape with cutting teeth or a new shape for the screw tip – each improvement translates into high usability of the screw in various applications.
You will find two types of the new induction-hardened R-HLX concrete screws in our range: the R-HLX-CS-ZF, a concrete screw with a countersunk head, and the R-HLX-HF-ZF, a concrete screw in flake zinc with a hexagonal head.
R-HLX concrete screw – innovations that can be seen
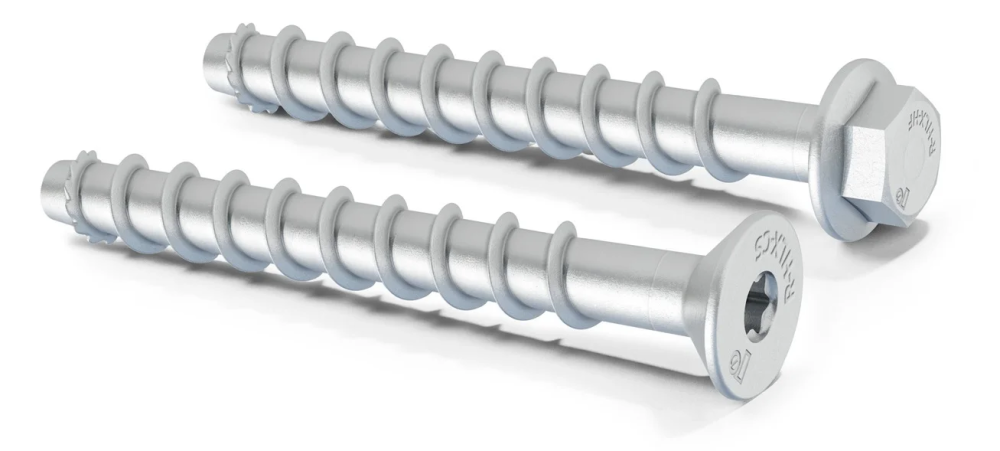
Features and benefits
- Unique single thread with pronounced profile pitch – responsible for ease and speed of installation.
- Sharp thread edge – maximises undercutting and facilitates installation in harder materials.
- Thread end with additional cutting teeth – ensures fast and easy installation, also in reinforced concrete C20/25 – C50/60.
- Optimised tip shape and notches on the thread coils – means effective anchoring from the start of the thread.
- Different head types – allows optimum adaptation of the screw to the fastened component.
- Zinc-flake coating – corrosion resistance of 800 to 1,500 hours.
R-HLX concrete screw – why is it worth it?
Structural changes are technical features. With the innovative form of the new R-HLX concrete screw, you get everything you would expect from a fastener for this type of application.
R-HLX concrete screws are:
- Highest load capacities – achieved through an even distribution of forces along the entire screw, which translates into a distribution of forces in the substrate.
- Structural strength – achieved through induction hardening, ensuring high hardness and high impact strength of the core.
- Effective undercutting of the base material – allowing screws to be installed close to edges and at short distances from other fixings.
- Seismic category C1 and C2 – allowing use in earthquake-prone areas.
- Fire resistance of up to 120 minutes – enabling use in areas requiring fire resistance.
- Polish production – the screws are manufactured in one of the largest, reputable cold forging factories in Europe with experience in the automotive and design industries. The steel for the R-HLX screws also comes from a Polish factory.
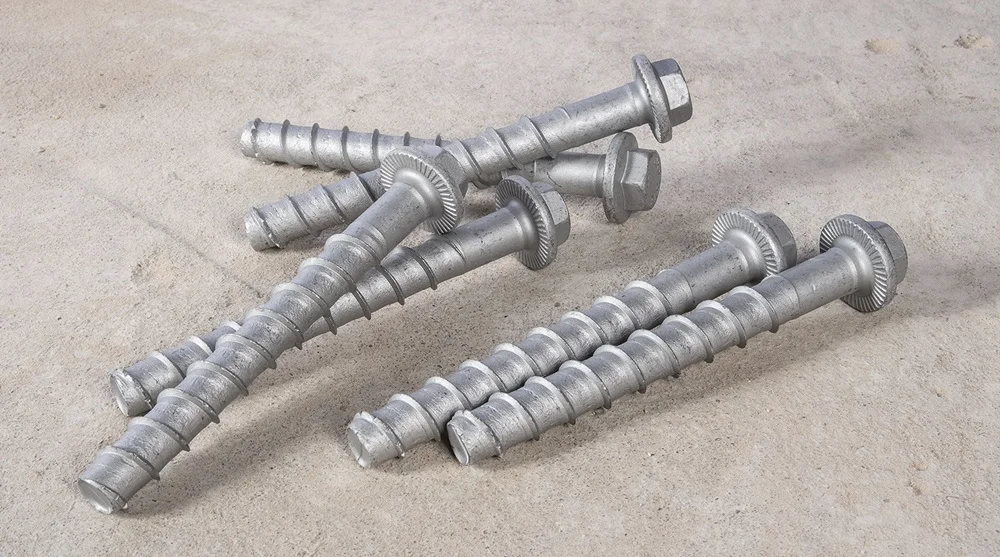
What to use R-HLX concrete screws for?
Concrete screws achieve a high capacity to carry increased loads due to the undercutting action of the base material through the sharp edge of the thread. This is a fundamental characteristic that distinguishes them from classic mechanical anchors, which obtain their load-bearing capacity on the basis of expansion mechanisms. This feature is the basis for the versatility of use of R-HLX concrete screws.
Concrete screws achieve a high capacity to carry increased loads due to the undercutting action of the concrete through the sharp edge of the thread. This is a fundamental characteristic that distinguishes them from classic mechanical anchors, which obtain their load-bearing capacity on the basis of expansion mechanisms. This feature is the basis for the versatility of the R-HLX concrete screws. What’s more, the construction of the screws is designed so that the effective anchoring depth starts in the concrete from the very beginning of the anchor, and by applying the thread to the end of the anchor length, we ensure better interaction with the substrate, thus achieving higher load capacities.
Where will R-HLX concrete screws perform well? In temporary installation, where it is possible to remove and reuse the screw after verification of thread wear using a tester. For installation close to the edges of the concrete – they guarantee the durability of the installation without disturbing the substrate. In close proximity to other screws – provide installation security in installations close to other screws, in earthquake zones C1-C2, and in areas requiring resistance to elevated temperatures.
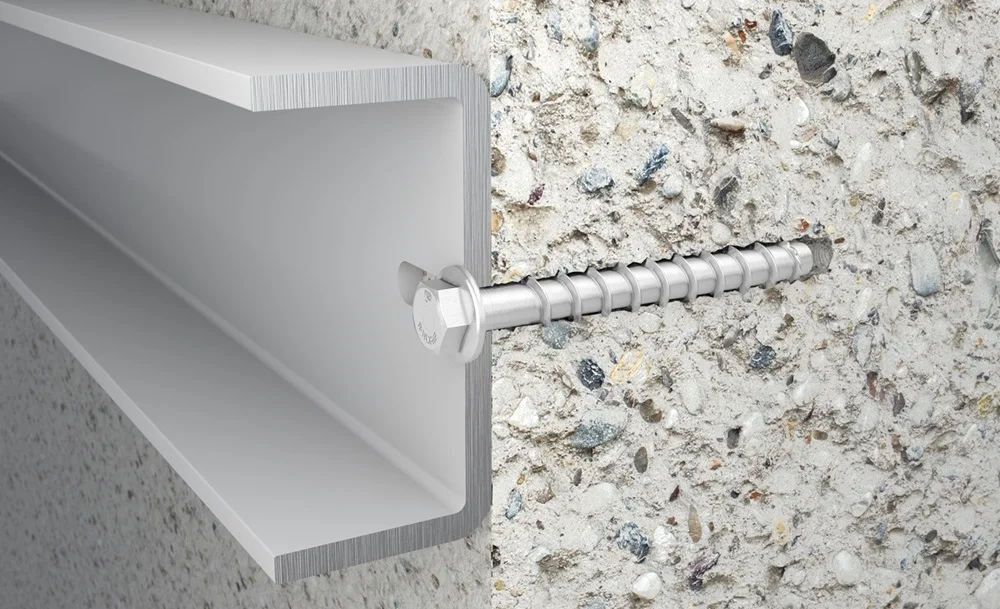
These are the applications that make the R-HLX concrete screw the perfect solution for fixing to cracked and uncracked, reinforced and unreinforced concrete substrates, as well as stone substrates of components such as traffic posts and signs, railings and balustrades, seating in public facilities and steel structures of various types.
It is a one-piece fixing and neither washers nor nuts are required. What’s more, installation of the screws does not require any special tools – a tangential impact screwdriver, such as the R-PID18, is sufficient. If necessary, it is possible to remove them completely, without invasion.
The following types of R-HLX screws are available for sale:
- R-HLX-CS-ZF – flake zinc plated concrete screw with induction hardened countersunk head
- R-HLX-HF-ZF – flake zinc plated concrete screw with induction hardened hexagon head